HPM200 CWS
Base | CAT®330 |
---|---|
Drilling Depth | 155' ft47 m |
Drilling Diameter | 2400 mm8' ft inc |
Operating Weight | 128300 lbf60000 kg |
Rotary Effective Torque | 185000 lb.ft251 kNm |
A first-of-its-kind Crowd Winch Machine
The HPM200 Crowd Winch System has been designed to drive long casings in challenging ground conditions.
Key feature is the Revolutionary Dual Winch Crowd System.
A first-of-its-kind system featuring two dedicated winches, coaxially mounted, for pull and push functionalities.
HPM200 CWS
A first-of-its-kind Crowd Winch MachineThe HPM200’s innovative crowd winch system design offers extended rotary stroke to maximize the reach of the rotary head for greater drilling flexibility.
The wire ropes for both pulling and pushing forces remain constantly under tension, minimizing slack and enhancing overall system efficiency.
It features an independent winches control, having the ability to operate the pull and push winches independently grants ultimate control during operation, inspection and maintenance.
When in CFA configuration, with the sheave in the very top part, the system efficiently store and manage wire rope on a second layer, ensuring smooth operation at great stroke.
The HPM200 are mounted on reliable CAT ® 330 NGH base, equipped with CAT® C7.1 engine, which delivers an ISO power of 205 kW (175 KW Fly Wheel).
Just like any HPM, this HPM200 CWS has a modular design allowing to be quickly converted from Standard to Low-Headroom configuration to tackle drilling projects under infrastructure, powerlines, substations, and other low-clearance environments with ease.
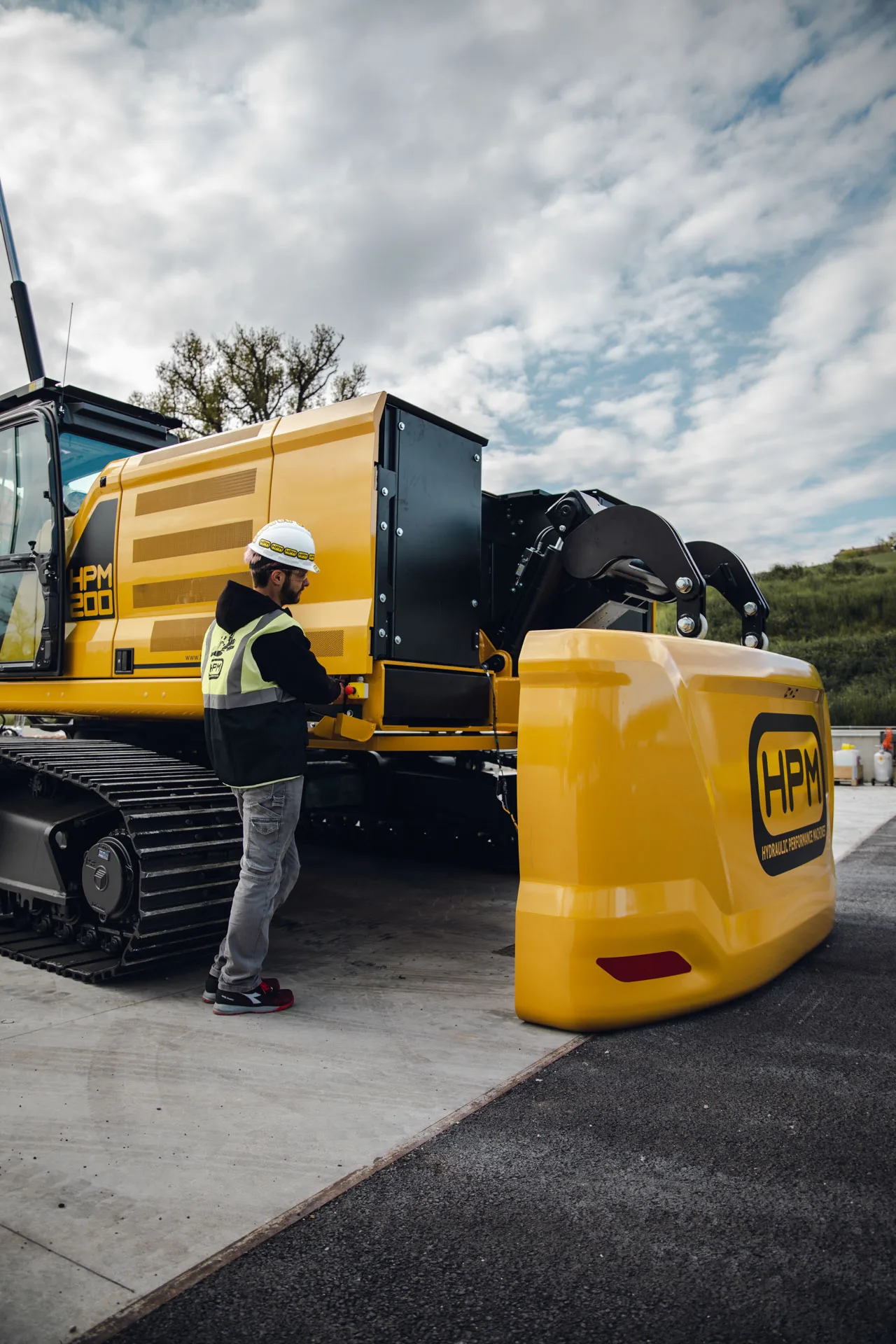
Counterweight Lifting System
This HPM can be assembled by itself without the need of assistant cranes.
This patented feature gives contractors the ability to quickly and easily reduce the overall weight of the rig during the transport phase, making it possible to utilise a standard-sized trailer and reduce then hauling costs and avoids oversize/overweight permits.
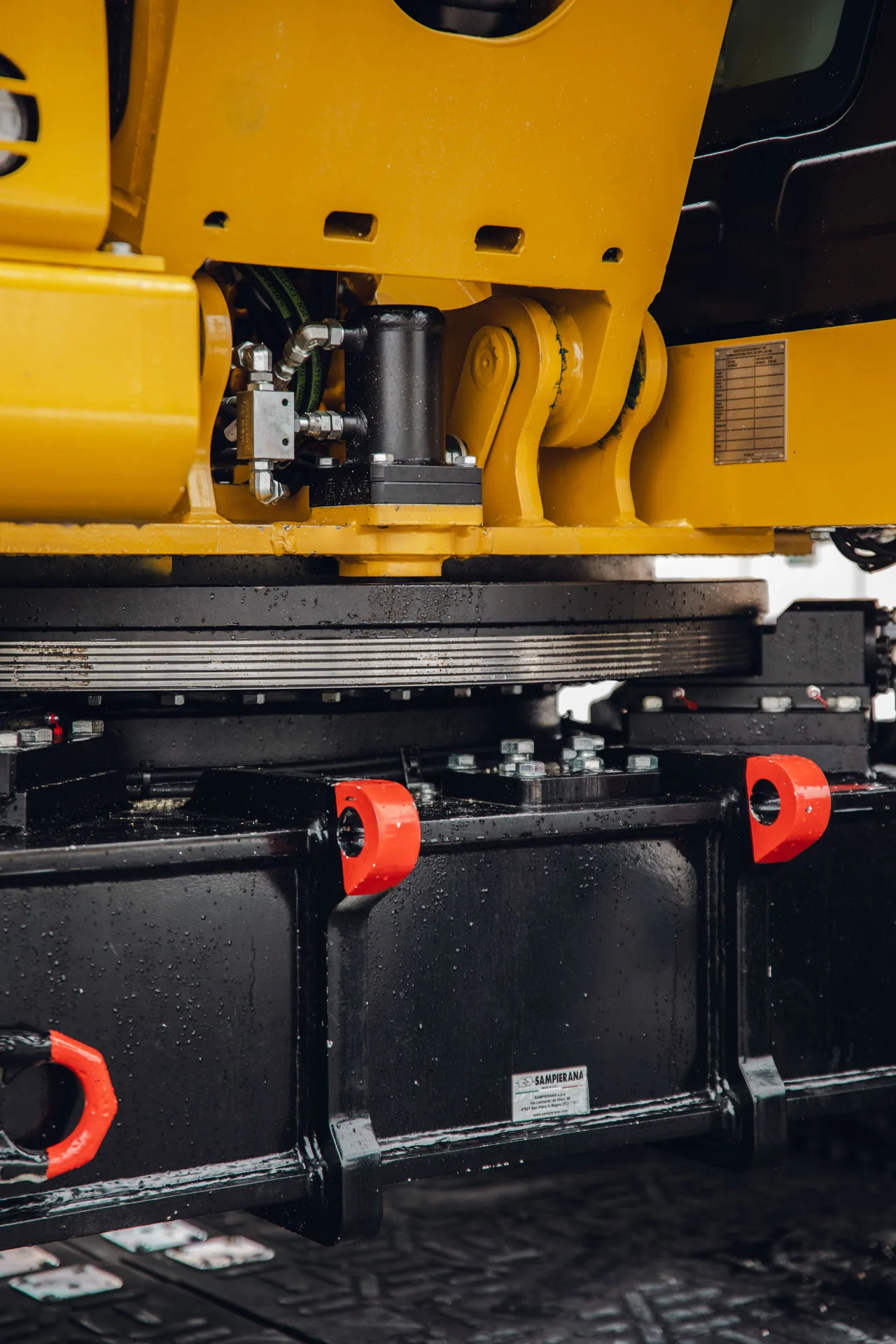
Auxiliary House Lock
The operator can make the full use of the whole torque without having the machine swinging from side to side.
This patented feature can be automatic or enabled through a button on the joystick. The enabling of the brake offers increased comfort for the operator as the vibrations when drilling on rock are reduced to almost zero.
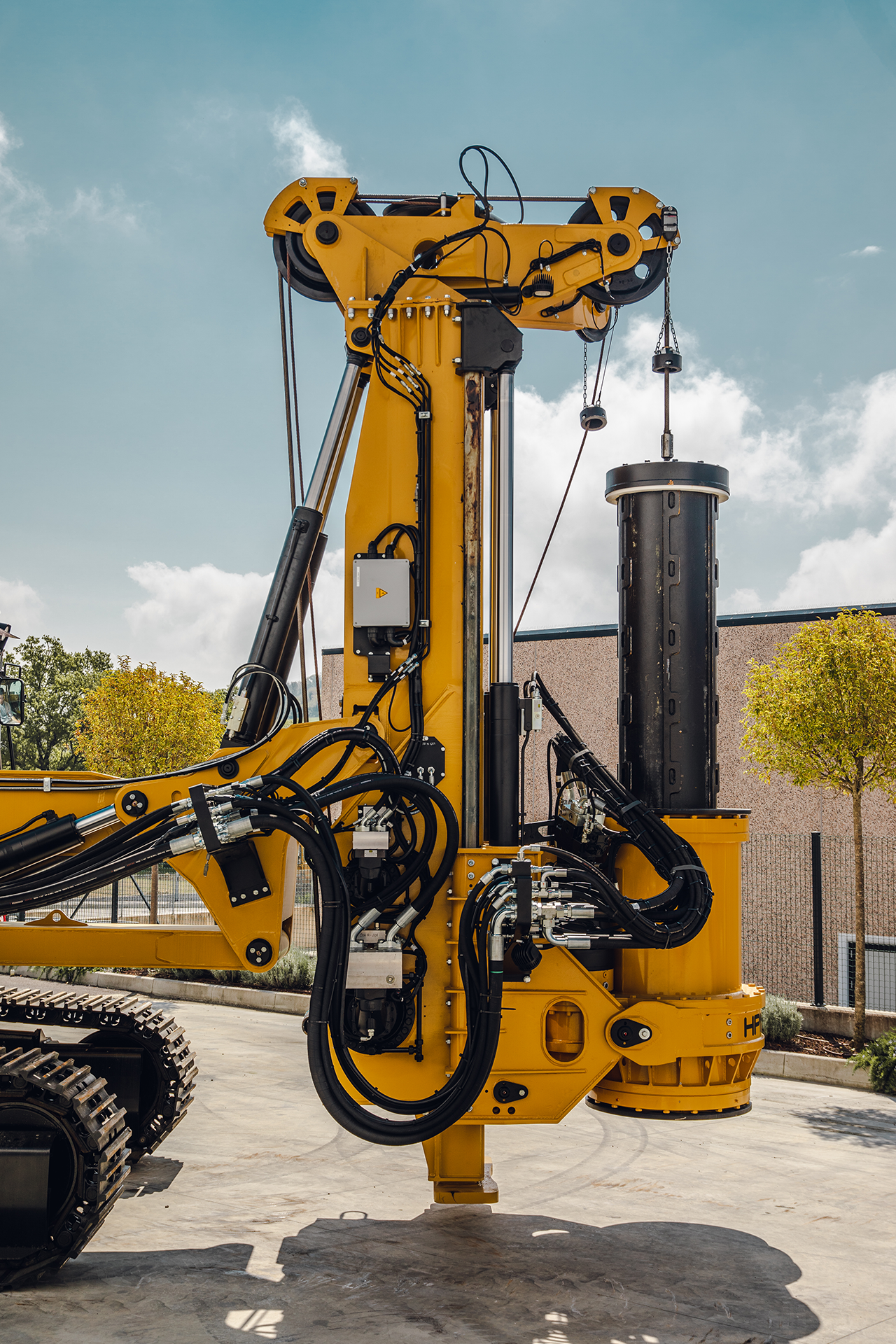
Low-headroom Configuration
This HPM can be quickly and safely converted in Short Mast configuration allowing it to work in limited heights job sites, such as under bridges or below power lines.
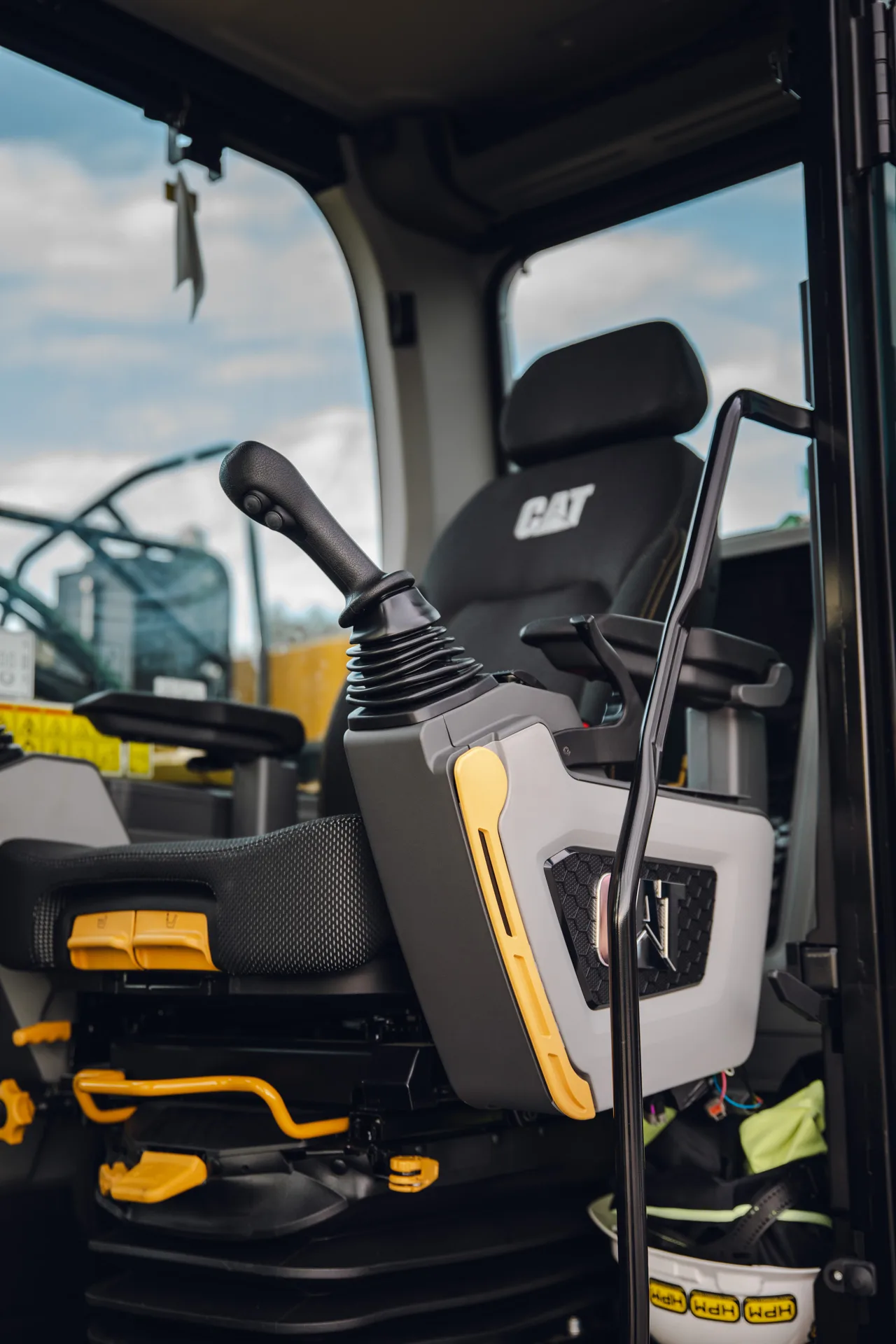
Comfort Cabin
The HPM cabin is equipped with a comfy and wide adjustable seat. The standard automatic air conditioning keeps the cabin at the ideal temperature throughout the day.
All machine interfaces are ergonomically positioned and designed for optimum control and efficiency. The easy accessible keyboards allow the operator to quickly get the rig ready to drill.
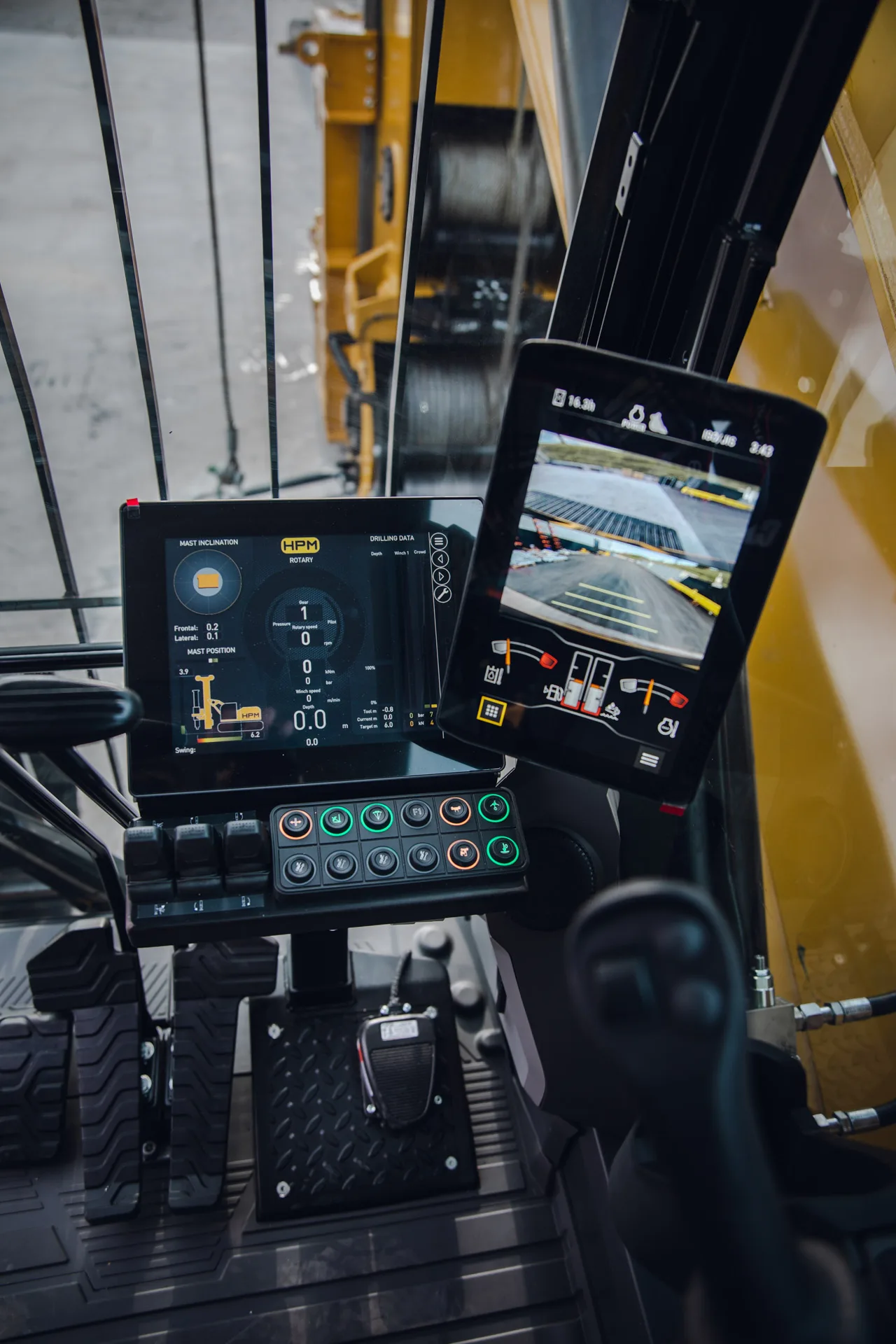
Automatic Functions
Automatic functions allow the operator to reduce rig-up time and get the most in productivity.
With a push of a button, the operator can make use of automatic functions, including: Verticality of the mast, Automatic Rig-up, Automatic return to drilling point and rotary auto drive.
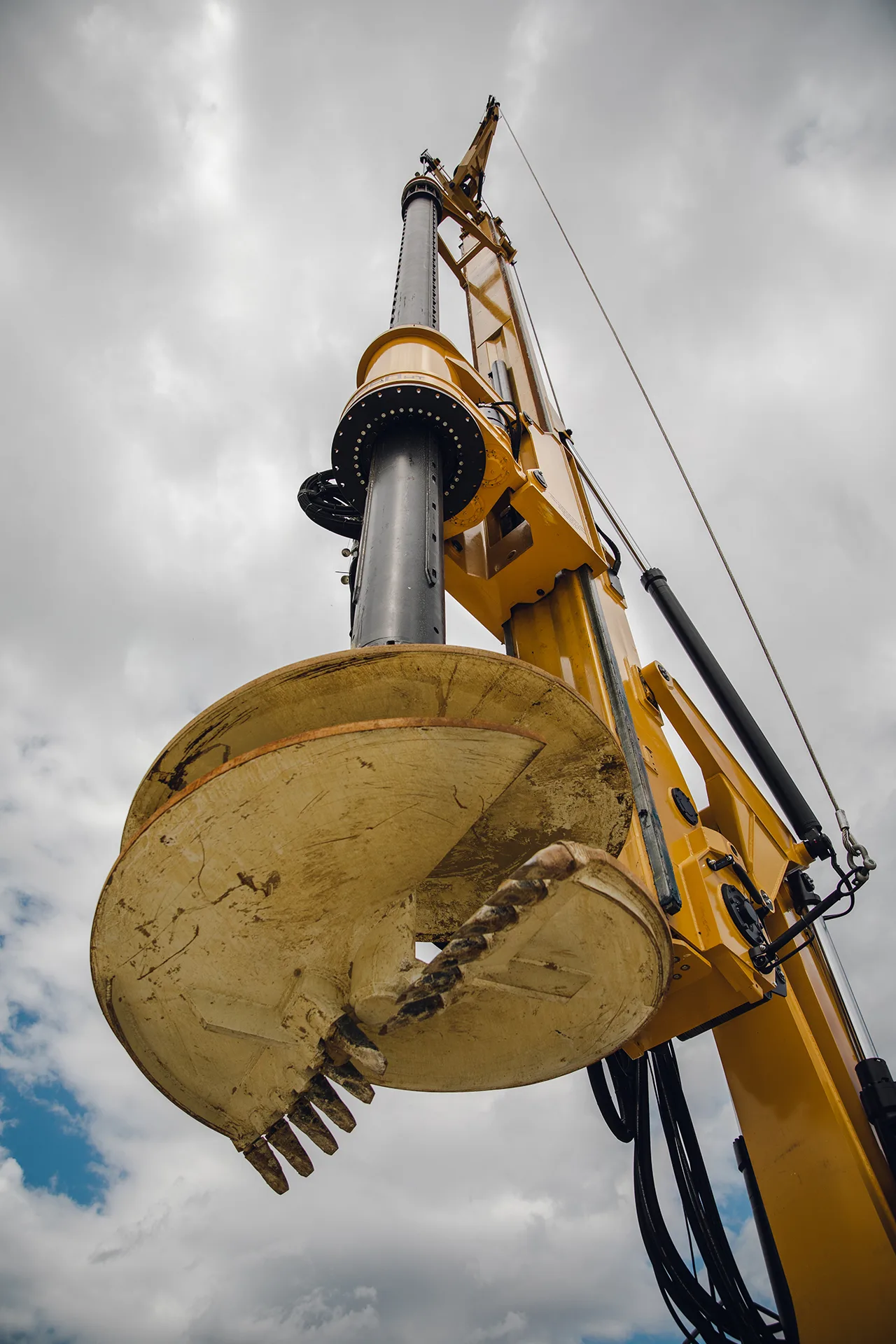
Drilling Cruise Control
The HPM software includes the enabling of the drilling cruise control. When the system is enabled, the operator can preselect the rotary gear so it’s speed. With a push of a button the system can be activated and the operator can also lock the crowd pressure for a complete automatic drilling mode. Safety systems can disable the function immediately.
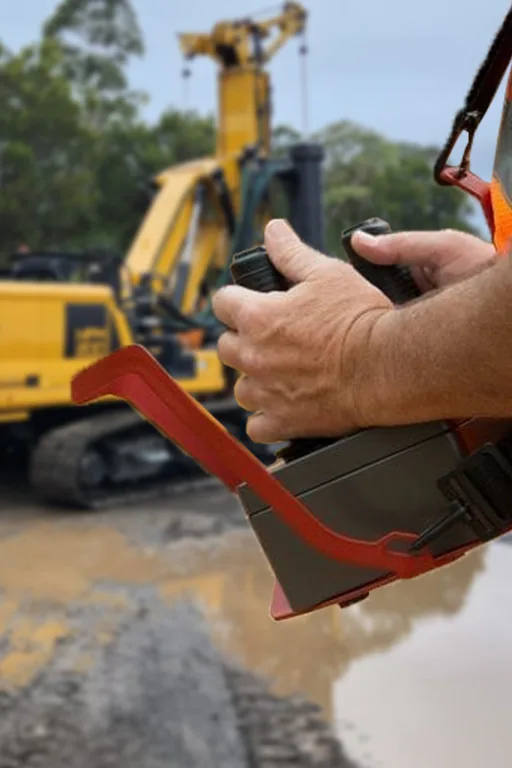
Remote Control
Increase safety and flexibility when loading or unloading the equipment. The operator can make use of different viewing angles while moving the machine from outside the cabin. Having a complete view of the rig during these phases allows the operator to make sure that hoses, wirings and wire ropes are safely positioned. Drilling functions are enabled through the remote control for a safe service and maintenance of the rig.
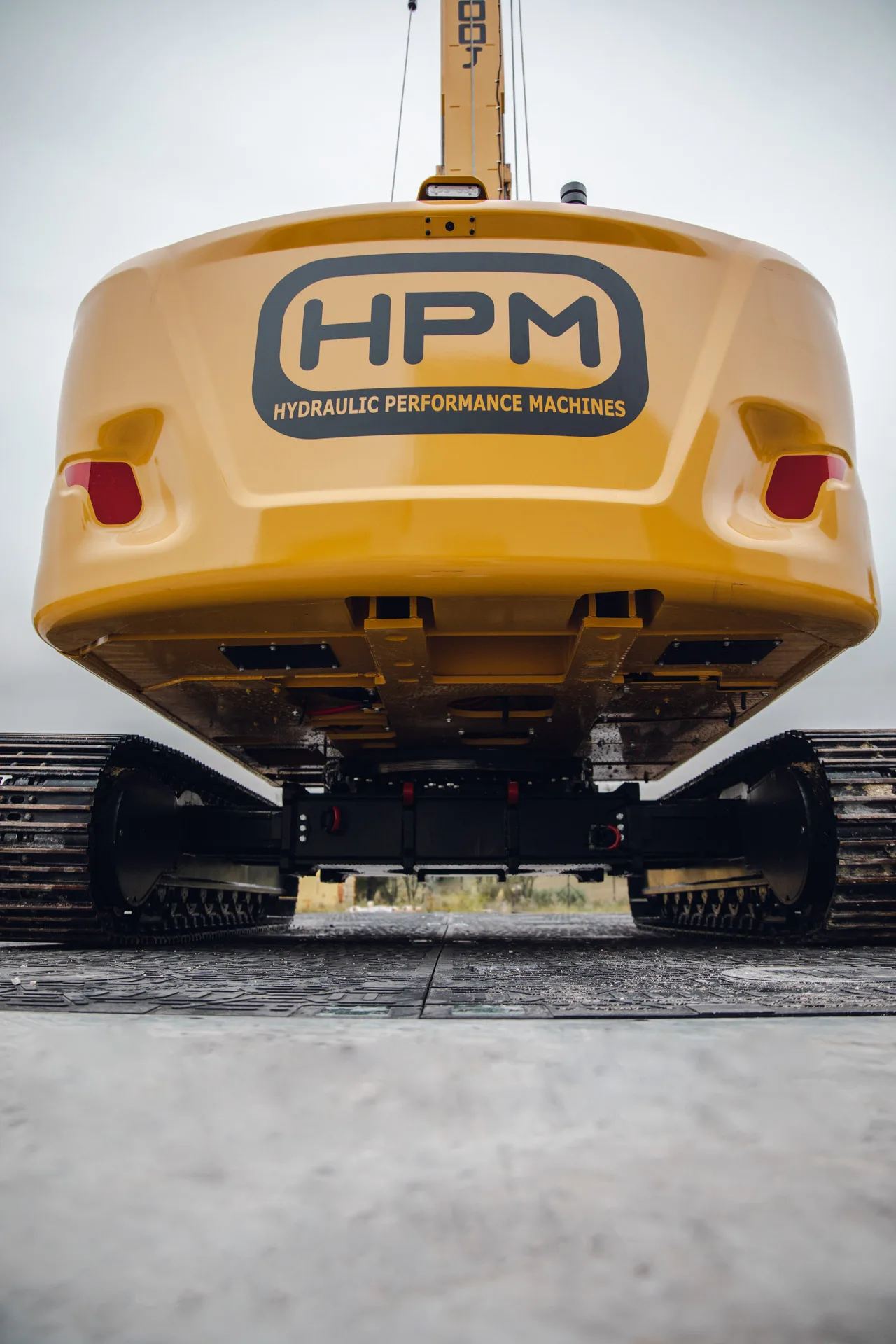
Expandable Tracks
The retractable undercarriage allows to reduce width of the machine for transport phases, reducing hauling related costs and avoiding transport permits. Once expanded, the undercarriage provides great stability at any working radius for a 360° drilling capability.
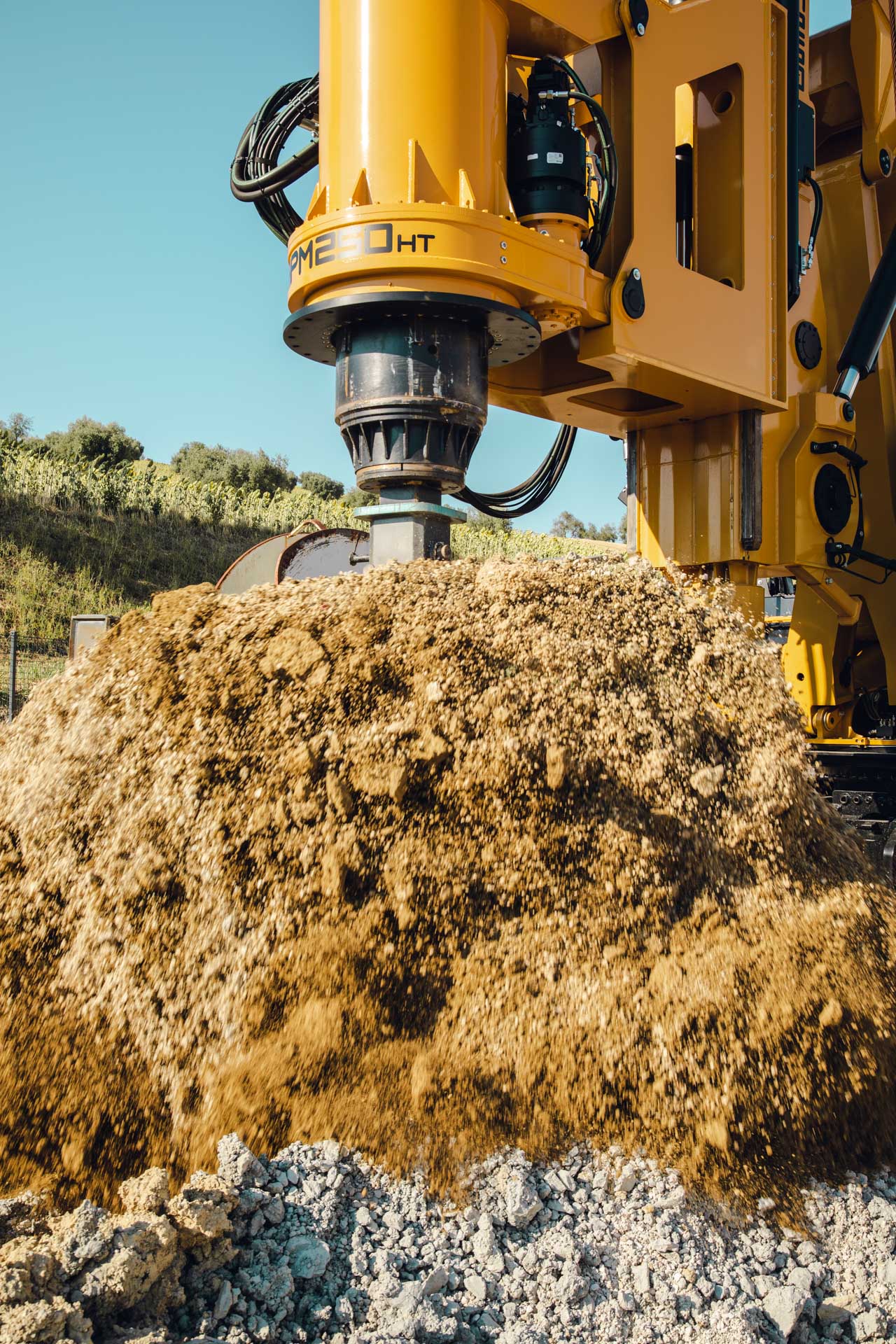
Rotary Gear System
During the working phase, the operator can choose the right rotary rotation speed, having 10 speeds available.
The HPM patented rotary gear control system allows the operator to quickly reach the optimal spin-off speed, with just one click.
Technical data
All data presented refers to the standard model and may vary based on specific equipment configuration and customer requirements.
Need more torque, pull or depth? Contact us to explore the full range of configuration options.
Base | CAT®330 |
---|---|
Engine Type | C7.1 |
Installed Power | 205 hp275 kW |
Max. Effective Torque | 185000 ft.lbs251 kNm |
---|---|
Working Speed | 7-24 rpm |
Discharge Speed | 45-80 rpm |
Main winch pull | 230 kN51700 lbf |
---|
Crowd Type | Winch Crowd System |
---|---|
Max. crowd force | 310 kN70000 lbf |
Crowd Stroke | 26'4" ft inc8150 mm |
Drilling Depth | 155' ft47 m |
---|---|
Drilling Diameter | 2400 mm8' ft inc |
Operating Weight | 128300 lbf60000 kg |
---|---|
Transport weight | 36500 kg80500 lb |
Transport width | 3000 mm9'10" ft inc |
Transport height | 11' ft inc3380 mm |